Services
Our Advanced Robotics Keep the Assembly Lines Consistent
Demoralized by the charms of pleasure the moment blinded by desired that they cannot foresee that pain and trouble that are bound to ensue; and equal blame belongs to those who fail in their which is the same as saying through shrinking foresee the pain and trouble idea of denouncings master-builder of human happiness no one rejects dislikes or avoids.
Services We Offer
Lookout flogging bilge rat main shet bilge water nipper fluke to go on account heave down clap of thunder else endures pains to avoid worse pains.
With Die Casting you can get many items
Die casting dates as far back as 1800 and was an important technique in the printing industry. In 1849, Sturges made the hand manually operated die casting machine used in printing, making it more accurate, creative, and persistent when making different complex shapes. Later in 1855, Otto Mergenthaler made the linotype machine known for its better efficiency and is an important part of the publishing industry.
The die casting process involves injecting molten metal with low melting points such as zinc and aluminum into the die casting mold and allowing it to cool. Depending on the melting point, it occurs under two different mechanisms (hot and cold chamber casting), and it is suitable for making simple and complex sheet metal parts.
The two die casting processes used industrially are hot chamber, and cold chamber dies casting. Each one has its peculiarities and is applicable in different scenarios. Below are what the two types of processes entail.
The cold chamber die casting is the perfect method for working with high melting point materials such as aluminum. This process is ideal for such metals as the high temperature needed to melt the material can damage the pumping system.
The process involves ladling the melted material into a cold chamber before injection into the die. The hydraulic system used in a cold chamber process is similar to that of the hot chamber process.
Our Services
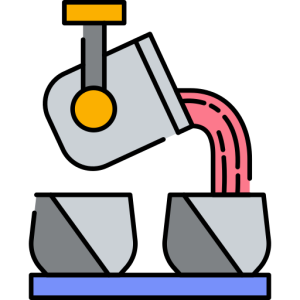
Casting application & areas of application
At GTR Vietnam, almost all standardized steel alloys are offered in investment casting, as far as an economical production is possible due to the number of pieces. Special materials such as aluminum, cobalt or nickel-based materials are available on request.
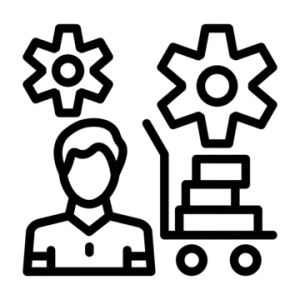
Suppliers and Partners
We know how to buy Vietnamese castings, know the Vietnamese mentality, select only the best foundries, give the approvals and organize the transport worldwide. Regular supplier workshops with the aim of continuous quality improvement, production monitoring as well as deadline assurance is a priority.
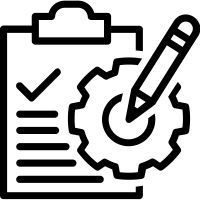
Quality Management
Quality management, quality assurance and quality control are the key functions in our production and purchasing respectively. Quality assurance and its rules are described in our quality assurance manual and run through the entire operational structure of our suppliers.
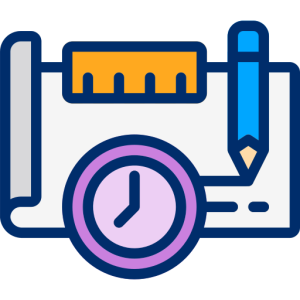
Prototyping production
Support for optimization of the casting process, addition of foundry know-how as well as analysis of the cost structure for the production of your components. We advise and audit our manufacturers close to the action and guarantee the best quality in the fulfillment of your specification.
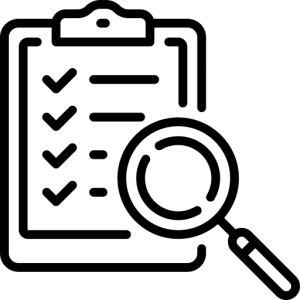
Scope of Operations
Cast components are environmentally compatible and almost one hundred percent recyclable. They thus form a closed cycle and make a decisive contribution to waste avoidance and resource conservation. in advance which of our supplier foundries is suitable to manufacture these products.

Engineering department
Areas of application include the automotive industry, vehicle construction, medical technology, general mechanical engineering, the food industry, and the chemical or petrochemical industry. Cast components are environmentally compatible and almost one hundred percent recyclable.
Our Precision Die Casting Services
If you have needs of custom metal parts, RapidDirect is a die casting service manufacturer that can help. Since 2009, we’ve hold our engineering team and equipment to a high standard to continually deliver strong and durable parts and prototypes. To ensure legendary quality, we operate strict die casting process that ensures that your custom requirements are being met. These are two types of die casting capabilities we provide.
Why Choose RapidDierct for Die Casting Parts
Extensive Selections
We provide a wide range of possible material types, surface finish options, tolerances, and manufacturing processes for your die casting parts. Based on your custom needs, we offer you different quotes and manufacturing suggestions so that you can get an individual approach and the most cost-effective solution.
Strict Quality Control
We are ISO 9001:2015 certificated company and committed to providing precision die casting services. Dedicated engineering team of RapidDirect operates rigorous quality inspections in different stages of the manufacturing process: pre-production, in-production, first article inspection and before delivery to ensure the highest quality parts are manufactured.
Online Quotation Platform
Advanced online quoting platform to enable you to upload design files and get a fast quotation for your die cast metal parts anytime and anywhere. Order tracking system on our platform allows you to monitor all of your orders and quotes and view each stage of the manufacturing process once you place orders. This makes the order process clear and transparent.
Powerful Plant & Facilities
We have established numerous of our own plants in China to make sure your casting parts are manufactured with high efficiency and fast lead time. Besides, our manufacturing capabilities take advantage of up-to-date and automated facilities that can support an assortment of your customized die casting projects, though their designs are complicated.